Researchers from Zhejiang University in China have used silver nanowires to fabricate transparent and flexible LED screens. The technique is both cost-effective and simple and can be applied when more opaque screens are not suitable. Additionally, in some situations existing screens can be too brittle when attached to a flexible surface.
The new discovery could lead to new capabilities for the technology industry, such as screens built into clothing or displays that are constructed in walls or windows.
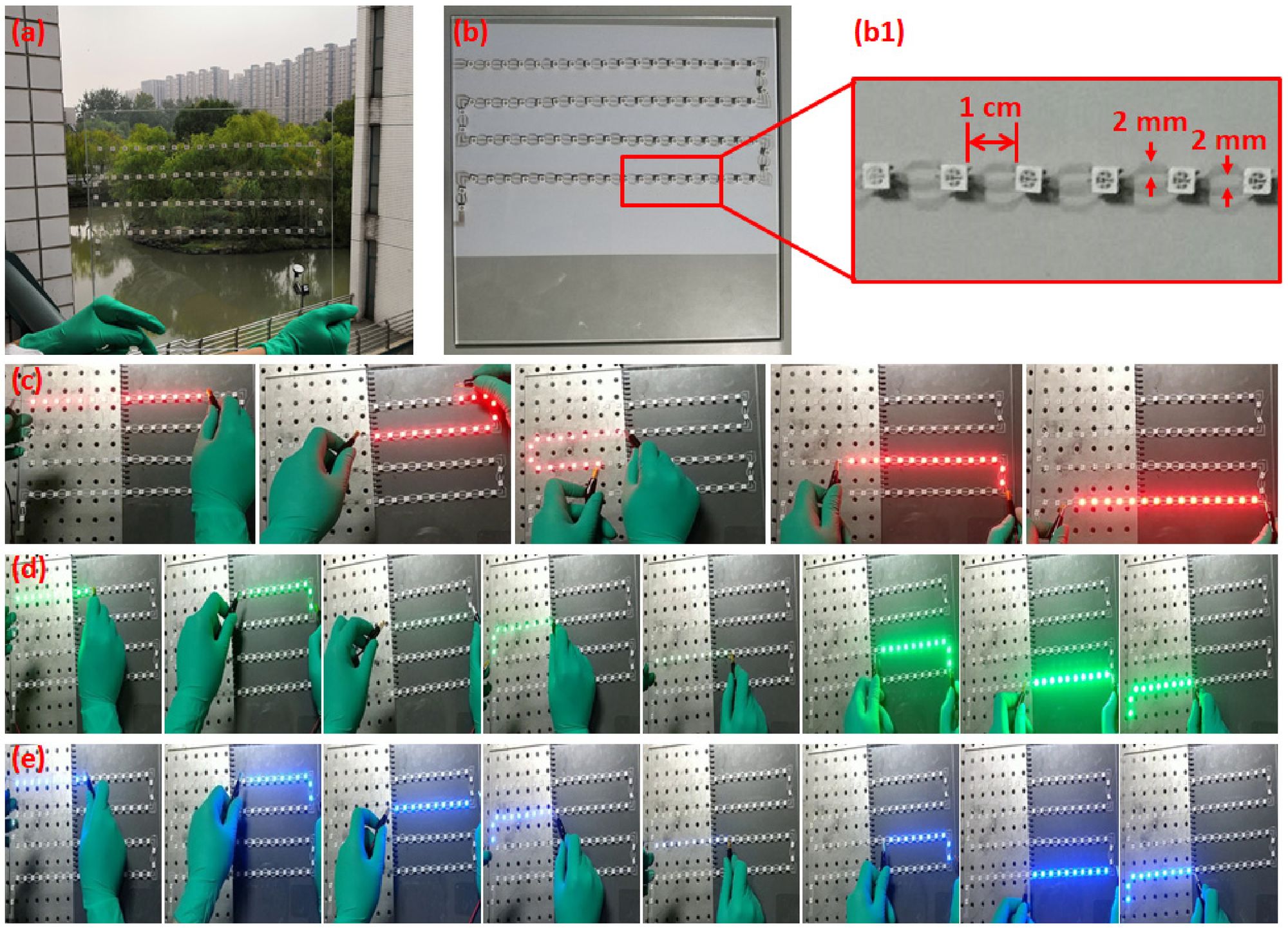
For many years, researchers have been looking at ways to make more flexible screens. Most studies looked at ways to adapt glass or clear plastic and involved networks of highly transparent electrical circuits that connected different LED parts together. The circuits on larger screens were made with either indium tin oxide (ITO) or fluorine-doped tin oxide (FTO). However, this is a complex and costly process, using expensive raw materials, and results in screens that are still relatively rigid and prone to cracking.
The challenge for Prof. Liu Yang and his colleagues was to imbed a network of wires that was dense enough to carry an electric current, but also sparse enough to make the screen transparent.
Knowing that silver nanowires contained excellent conductive, mechanical, and optical transmittance properties, and can be easily synthesized and spread over a wide area, they began to explore ways of integrating them as a network onto surfaces.
As the journal Physics World explains, “To manufacture their nanowires, Yang and colleagues first coated plastic and glass substrates with sacrificial masks, etched with networks of straight lines. After treatment in a specialized solution, these lines became stickier than the rest of the substrates. A further spray-coating process led to silver nanowires forming only along these sticky lines, creating an intricate network.”
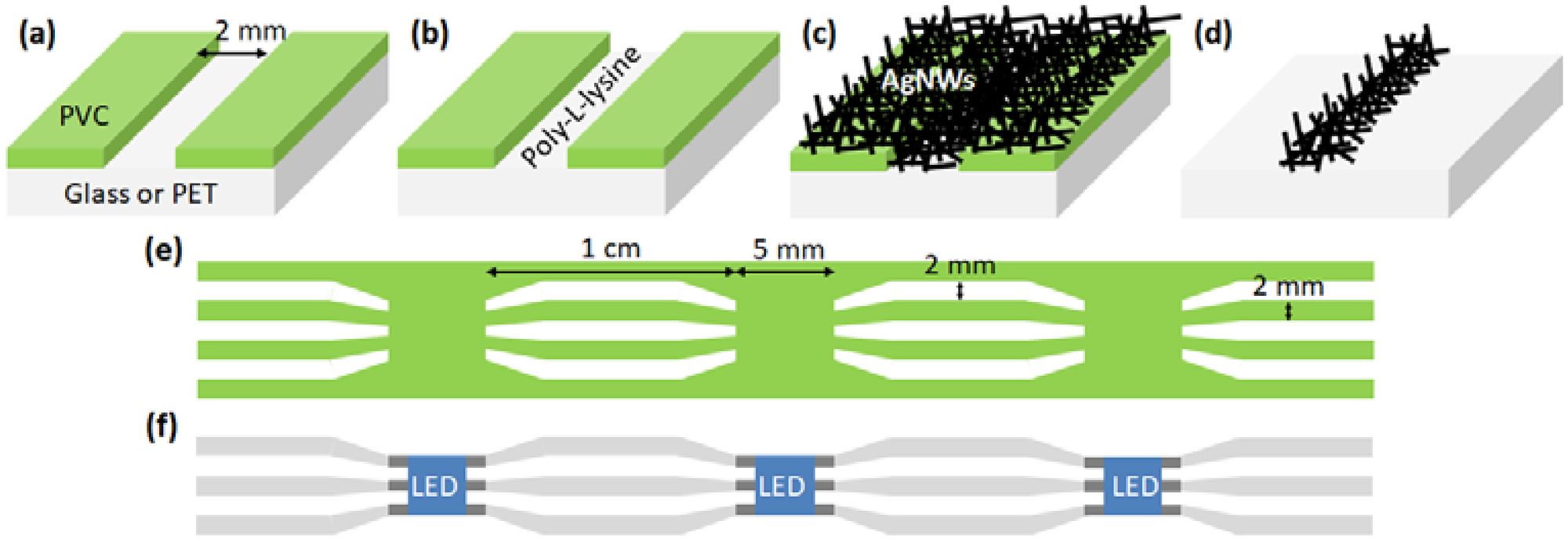
While previous studies had already been able to use nanowires as electrical networks, making long enough circuits for practical applications has proved challenging.
However, using this new technique the Zhejiang team were able to overcome the problem of length, fabricating a series of 25cm-long, transparent and highly uniform conductive strips.
Furthermore, “Through experiments, they showed that these strips possessed both high optical conductivity and low resistance, making them superior to previous tin oxide-based materials. In addition, they demonstrated a screen that hosted a silver nanowire circuit as long as 1.2m; enabling it to emit red, green, and blue light with varying biases, as seen in conventional displays. Finally, they showed that when the circuit was deposited onto a polymer substrate, its performance remained stable even when bent to a radius of 15mm - confirming its flexibility.”
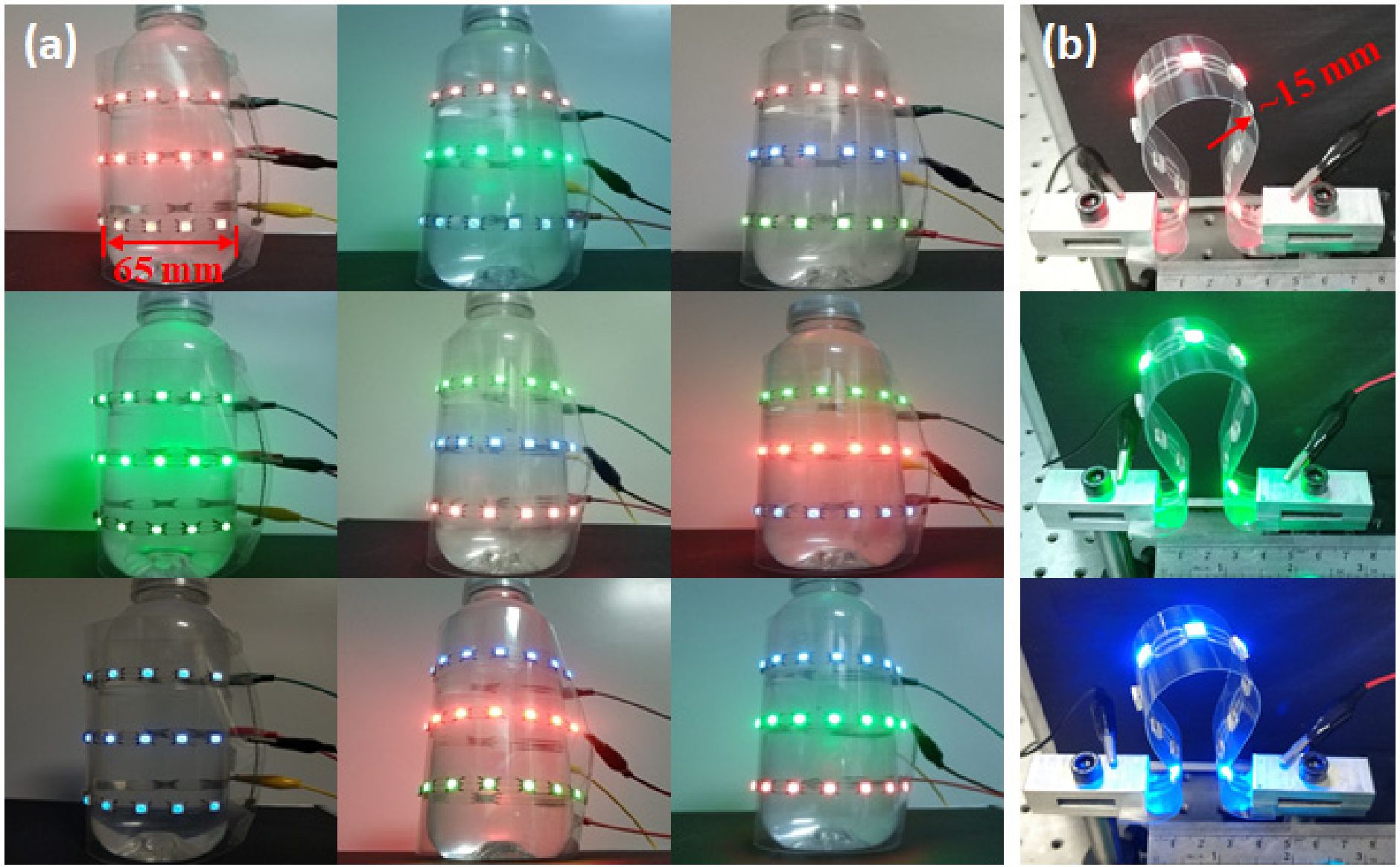
The team have now published their results in the journal Optical Materials Express, where they state their belief that this new nanowire method could replace tin oxide-based circuits in transparent display applications.
“Transparent LED screens act much like traditional LCDs or LED televisions but the fact that they don't block light enables creative applications not possible with conventional display technology,” said Yang, the study’s lead author. “The circuits we fabricated are highly transparent, conductive and flexible, and thus are very promising as a replacement for transparent circuits used today.”
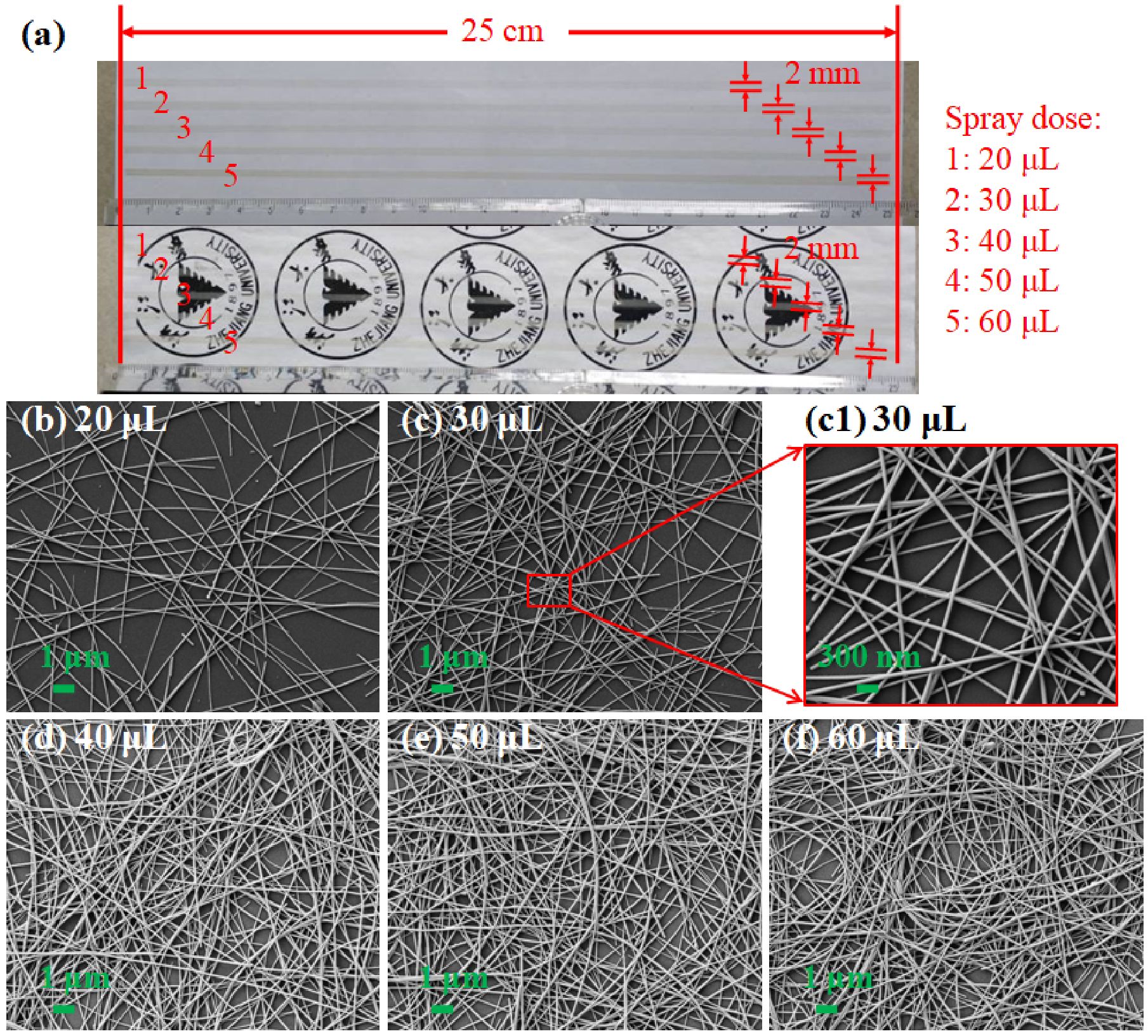
Moving forward, the researchers are examining different types of coating to better protect the circuitry, as well as developing improved substrate adhesion. Another avenue of study involves sandwiching the circuits between different materials for even sturdier protection. An approach that could potentially also allow for a simpler maintenance route if the material were easily removable.
Ultimately, silver nanowires make an ideal raw material for next generation screens, using their properties of strength, flexibility, electrical conductivity, and optical transference, all provided at a relatively low-cost.
“Because of our very simple and low-cost fabrication method and the inherent flexibility of silver nanowires, these new transparent conductive circuits could lower the cost and expand the applications of the transparent LED screens to ever more flexible and large-angle curved areas.”
Photo credit: Opticalmaterialsexpress