As soon as the first touchscreen mobile phones entered the market, it became apparent to consumers what their biggest flaw was; the glass screen breaks too easily.
Due to their flexibility and ‘shatterproof’ properties, some screen manufacturers experimented with plastic screens, but prototypes always found plastic to be too soft and easy to scratch. The hardness of glass made it the most durable and scratch resistant material, but still left it susceptible to breaking.
The situation improved drastically in 2005, when Apple and other top end phone manufacturers began using Gorilla Glass, a trademarked glass especially designed for phone screens. It was designed by the Kentucky-based company Corning and is made from a material called alkali-aluminosilicate which contains raw materials such as aluminium, silicon, and oxygen.
Despite the expensive raw materials and manufacturing process (the glass must be immersed in a hot potassium salt ion-exchange bath to further increase its surface strength and damage resistance), Gorilla Glass became a brand leader, and today is a feature on all major mobile phones.
However, the competition to find an unbreakable glass for the mobile phone market is intensifying as an increasing number of phones are now being made with glass backs as well as glass screens.
As Scott Forester, division vice president of marketing and innovation products for Corning noted in a recent interview, “More phones now feature glass not only on the front, but the back, with 28% of all phones sold this year and nearly 100% of all high-end phones featuring glass backs. With this development, it becomes all the more important for durable glass that can survive multiple drops.”
Additionally, research has found that current glass screen technology is insufficient for the way most mobile phone users handle their devices. As Forester says, “Consumers tell us that they tend to drop their phones, on average, about seven times a year, globally. And about half the time, it's from a meter or below. So, it made us start thinking about ever higher and higher drop heights.”
In response, researchers have turned to nanotechnology and the latest raw material science to meet market demand.
The result is that last month a breakthrough was made at the Rensselaer Polytechnic Institute, where a team of nanotechnology specialists found that silicon nanoparticles improved mobile phone screen glass performance, making it much less brittle and far less likely to break.
The team was led by Yunfeng Shi, an associate professor of materials science and engineering, and was based on the chemistry of glass at an atomic level.
As the journal Nanowerk outlines, “The glass currently used on many smartphones belongs to the oxide glass family, in which silicon atoms generally bond to four oxygen atoms. That type of bonding arrangement creates a rigid glass network that doesn't allow plastic deformation. So, when significant external stress is applied - as it is when a phone is dropped on a hard floor - the glass breaks.”
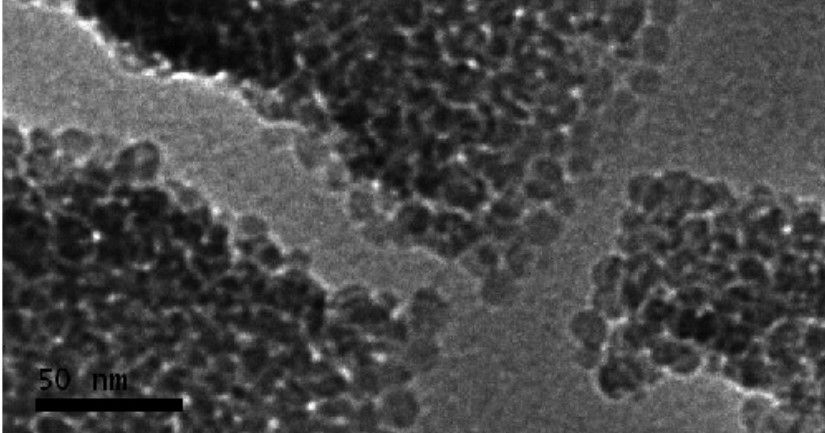
By using silica glass, made by compressing silica nanoparticles together, the team found that the glass could be stretched by up to 100% without breaking.
The researchers have now published their findings in the journal Nano Letters, where they state that, “… silica glass prepared by consolidating glassy nanoparticles exhibit remarkable tensile ductility. Because of dangling bonds at surfaces and high contact stresses, the pressure applied for consolidating glassy nanoparticles to achieve ductility is significantly lower than that required to toughen bulk glass via permanent densification.”
Additionally, as the journal Nano Magazine reports, “They also discovered that enhanced ductility emerges when silicon bonds with five oxygen atoms instead of four. This is known as five-fold silicon, and it's capable of shear flow under stress, … enabling the glass to withstand more load without fracturing.”
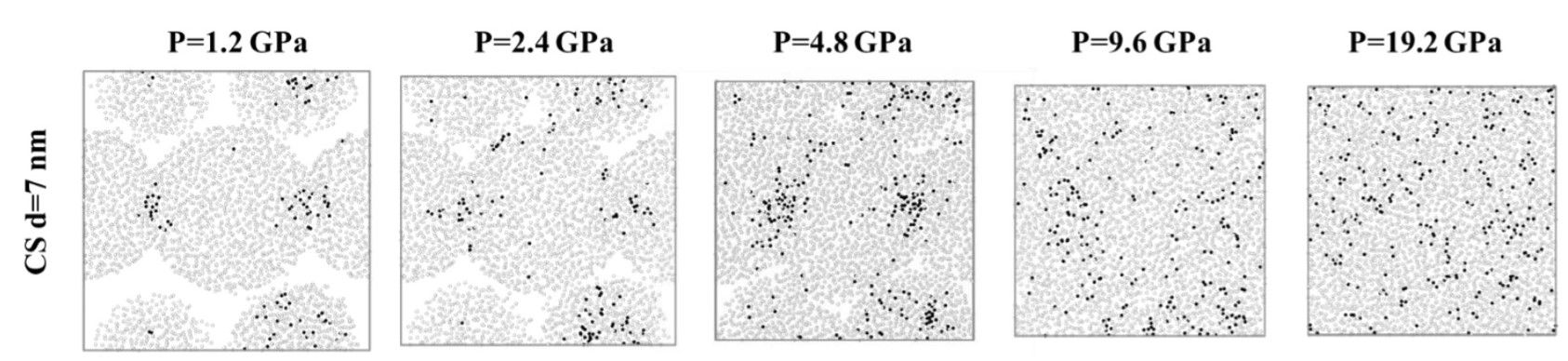
As Shi observes, “The compression actually changes the material structure.”
In fact, the nanomaterial glass is so strong, the team is looking at ways that it can be developed to work as more than just a glass.
“This glass is actually as stiff as steel. So, if the glass can be toughened sufficiently, it can replace steel,” Shi said. “Our holy grail is to make a transparent structural material.”
While further tests are required before buildings can be made entirely of nanoparticle silica glass, the research does add to the growing weight of evidence of how nanomaterials will shape industry and raw material selection in the future. Anyone who hasn’t yet learnt of the abilities of nanotubes, nanowires, and other nanoscale materials, may soon be looking straight through such unbreakable properties on their phones and tablets.
Photo credit: Eyerin, Nano Letters, Smartprix, Researchgate, Detached, Youtube, & Quora