While there are already thousands of practical applications for nanomaterials, research often focuses on finding ever more uses.
More recently though, nanotechnology specialists have begun to look at how to solve one of the biggest challenges for the nanotechnology industry; how to make cheaper nanoscale raw materials.
At the heart of this issue is that current techniques for producing 2D materials are ‘bottom up’. Processes such as chemical vapor deposition (CVD) and chemical synthesis which build nanomaterials starting with a single atom or molecule and getting bigger and bigger.
While these approaches are successful, they tend to produce very small amounts of nanomaterial, keeping costs high.
By looking at ‘top-down’ methods for producing nanomaterials, a team led by Professor Hui-Ming Cheng and Professor Bilu Liu from Tsinghua University have found a way to enable mass production of a wide variety of 2D materials, significantly driving down costs. The forms already made include, graphene, transition metal dichalcogenides (TMDCs) like MoS2 and WSe2, hexagonal boron nitride (h-BN), metal oxides (MxOy), and black phosphorene (b-P).
The new approach is based on the exfoliation of bulk layer materials to monolayer or few layer 2D materials.
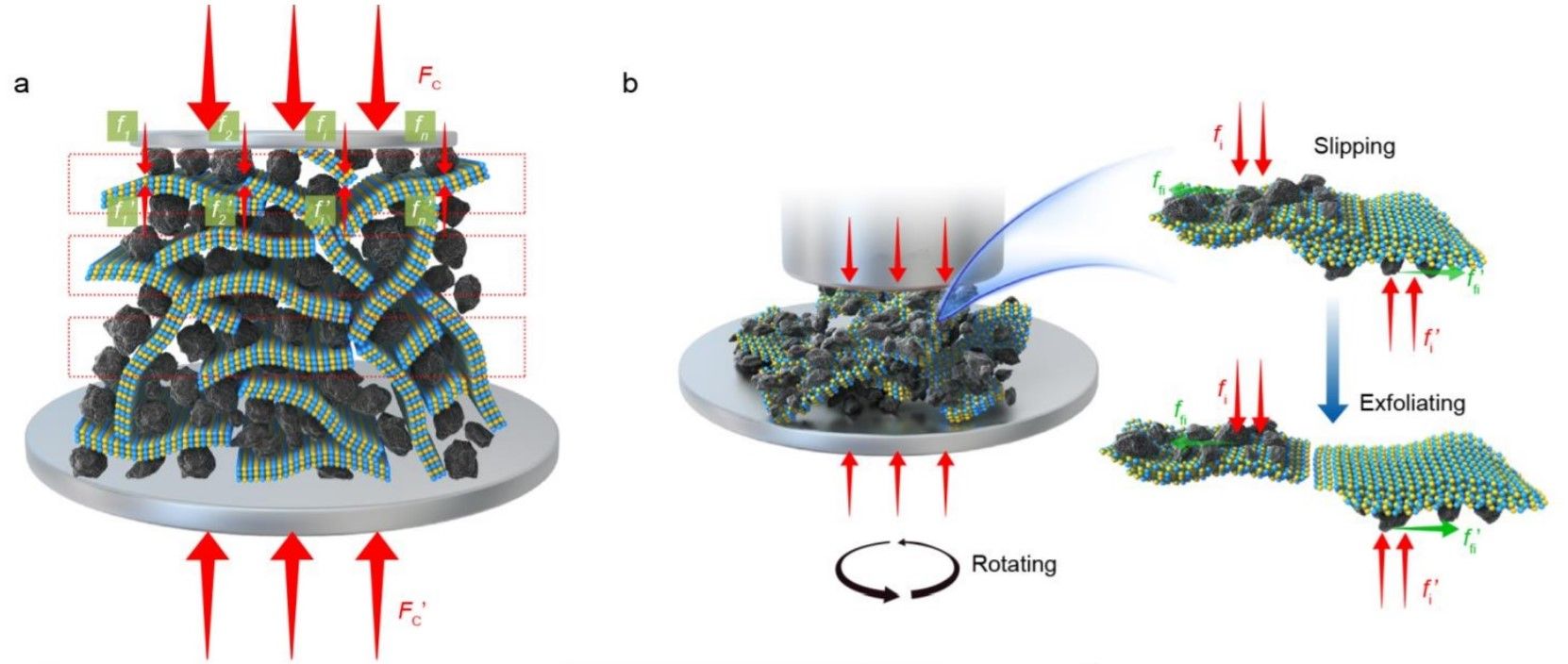
While similar techniques such as ball milling and liquid phase exfoliation, have already been developed, the team believe they have modified exfoliation in a way that can provide industrial scale nanomaterial production.
Currently, exfoliation techniques are only suitable for specific materials, with graphene and graphene oxide the only materials produced at the tons level. Making other substances suitable for exfoliating involved solving the problem of slipping.
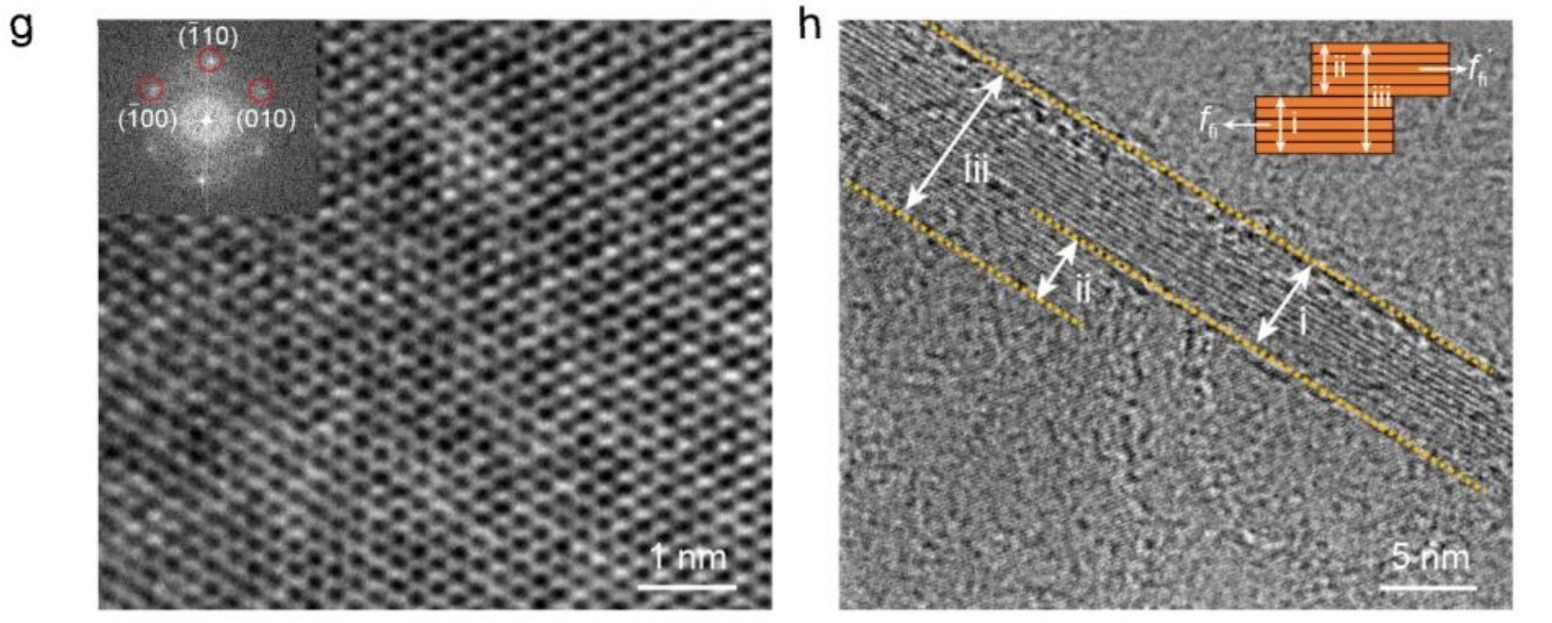
As the industry journal Nanowerk explains, “The failure of solid lubricants is caused by the slip between layers of bulk materials, and the result of the slip is that the bulk materials will be peeled off into fewer layers. Based on this understanding, … [Tsinghua University researchers] proposed an exfoliation technology which is named as interMediate-Assisted Grinding Exfoliation (iMAGE).”
Noting that, “The key to this exfoliation technology is to use intermediate materials that increase the coefficient of friction of the mixture and effectively apply sliding frictional forces to the layer material, resulting in a dramatically increased exfoliation efficiency.”
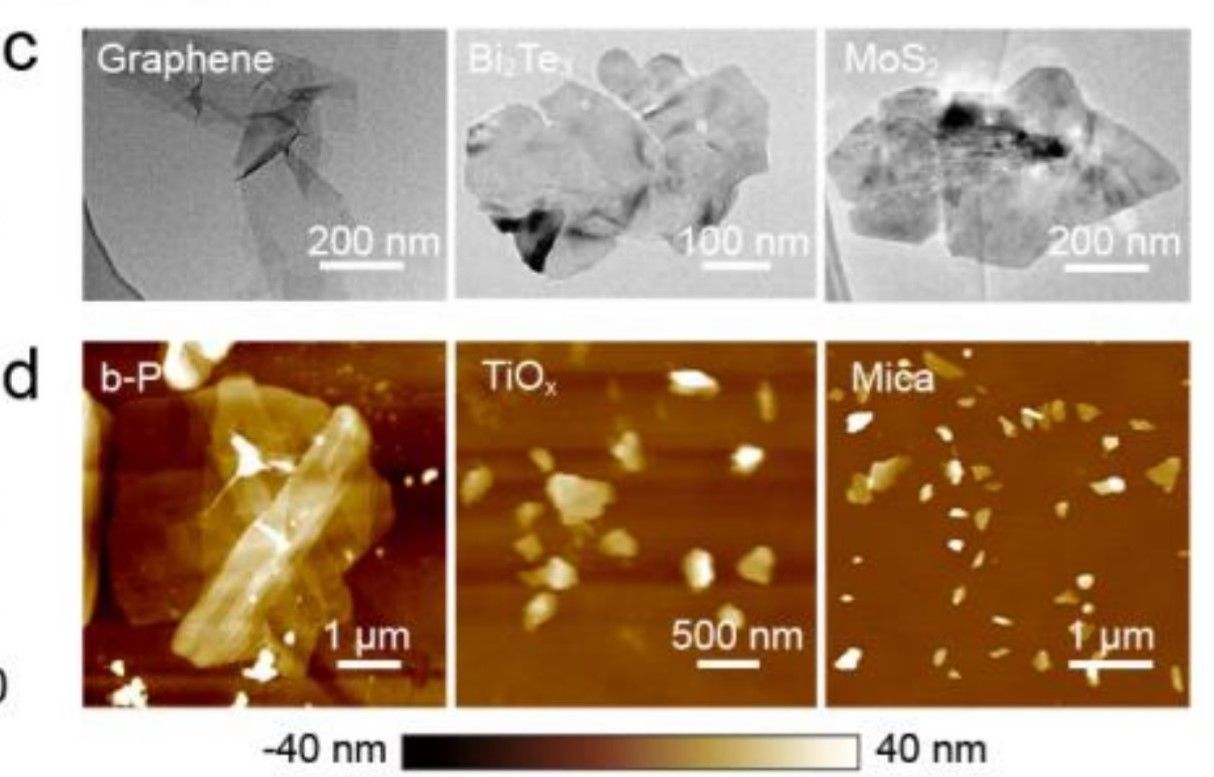
“This is the very first time that 2D materials other than graphene have been produced with a yield of more than 50% and a production rate of over 0.1g h-1,” says Liu. Adding that, “An annual production capability of 2D h-BN [hexagonal boron nitride] is expected to exceed 10 tons with our iMAGE technology.”
This was achieved with an average thickness of 4 nm and an average lateral size of 1.2 µm.
As the study, now published in the National Science Review notes, “… we have exfoliated bulk h-BN into 2D h-BN with large flake sizes, high quality and structural integrity, with a high exfoliation yield of 67%, a high production rate of 0.3 g h-1 and a low energy consumption of 3.01×106 J g-1. A production rate and energy consumption that are one to two orders of magnitude better than previous results.”
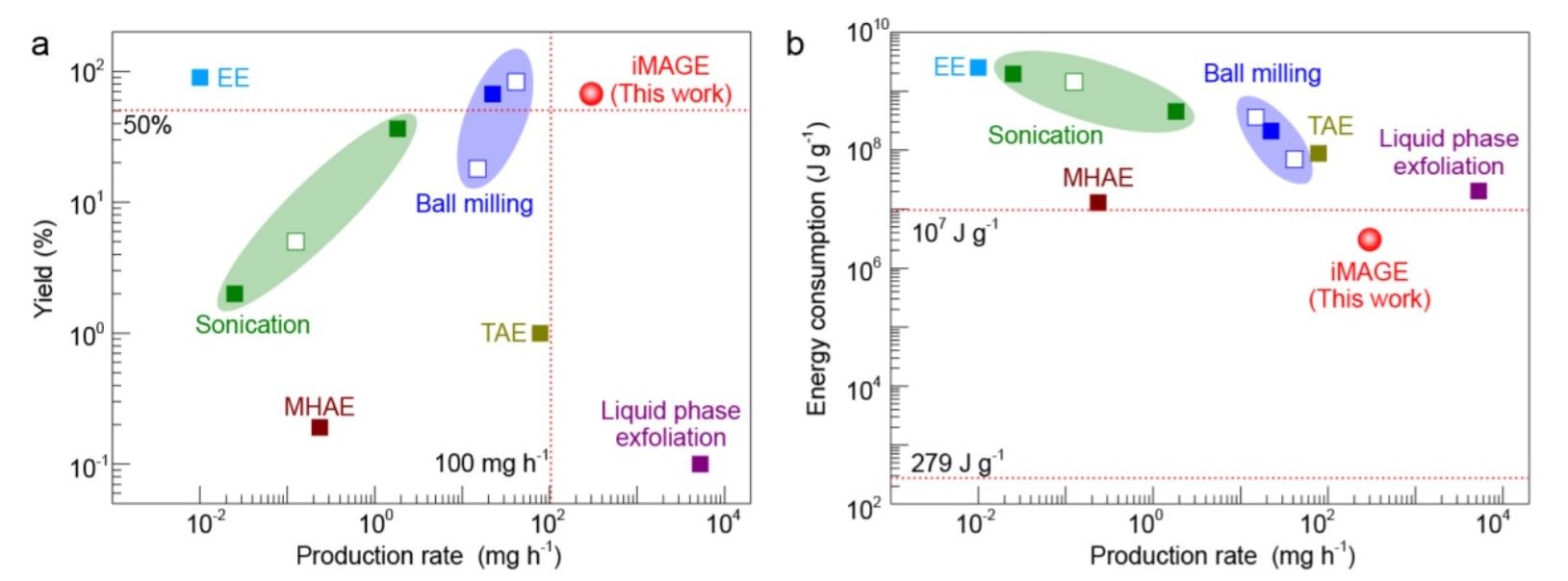
While the nanotechnology industry’s current ability to mass produce graphene and graphene oxide has enabled its commercial use in thousands of everyday products, increasing 2D raw material adoption has been hampered by a lack of economically viable production methods. By creating a scalable and energy efficient exfoliation technique, this research will open the door for widespread use of other ultrathin raw materials.
For example, included in the study’s tests was the use of molybdenite concentrate (as a natural low-cost mineral that is easily available) to produce 2D molybdenum disulphide flakes.
The team are now continuing their research to see how other substances react to the process, while also exploring commercialisation.
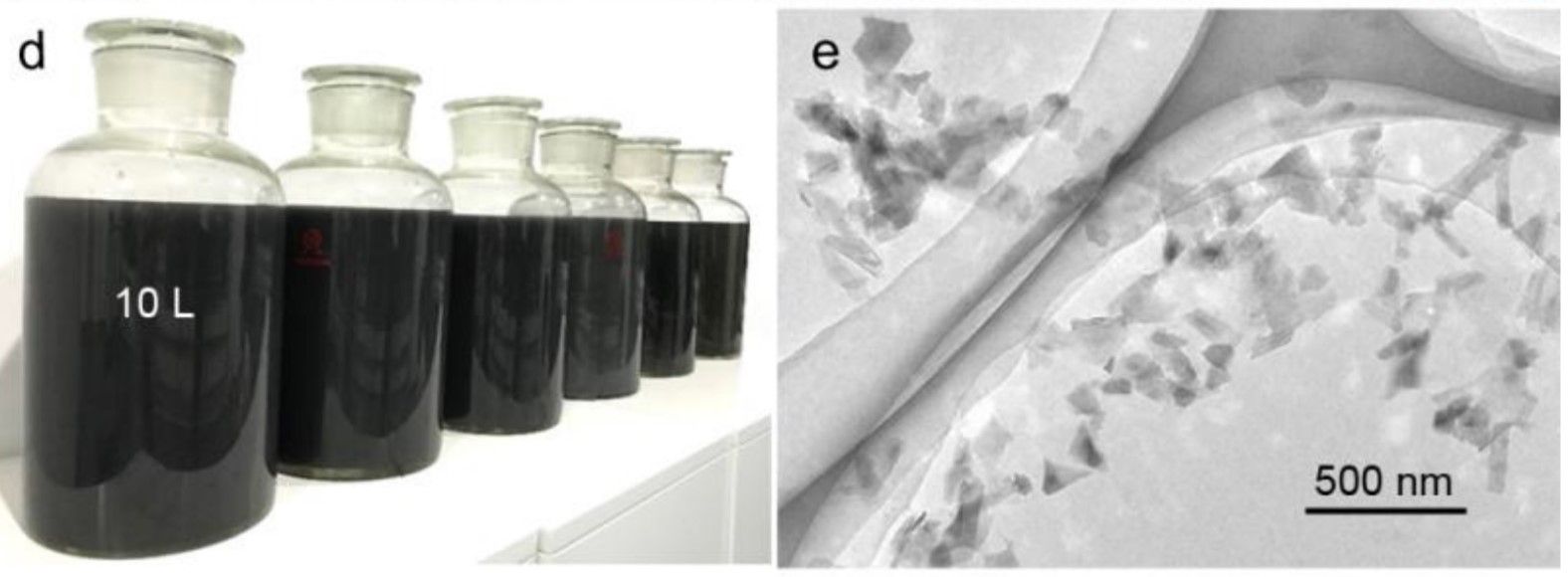
Ever since they were discovered, 2D materials have been promised as ‘the next best thing’. While to date this hasn’t fully materialised, they are widely used in small doses in numerous products. But bulk use in quantities as heavy as a tonne and even wider usage has always been limited by the ability to upscale production.
With this economically viable method, much of that problem seems to have been solved.
As Lui states, “iMAGE technology overcomes a main challenge in 2D materials, i.e., their mass production, and is expected to accelerate their commercialization in a wide range of applications in electronics, energy, and others.”
Photo credit: NationalScienceReview