Carbon black plays a key role in the manufacture of conventional car tires, but that may all be about to change.
In a standard tire, about 28% is carbon black filler, a soot-like reinforcing agent that is produced by partially burning fossil fuels). The other ingredients are natural rubber made from latex sap (28%), synthetic rubber made from oil (28%), and a complex mixture of other chemicals and agents (16%).
This makes tires a very non-sustainable product, full of fossil fuels and synthetic chemicals. They are also highly inefficient, as the rubber tread that is designed to help the vehicle grip the road also provides resistance that stops the wheel from rolling.
For years, carbon black has been known as a major cause of the problem, with chemical engineers and designers attempting to modify the ingredient to improve efficiency. As Scientific American notes, “The drive to produce low-rolling resistance tires was a first step toward making them more eco-friendly because it involved replacing certain petroleum-based substances in tire construction. Manufacturers added modified silica filler—essentially, surface-treated sand microparticles—to replace some of the carbon black reinforcement in standard tires.”
Producers and suppliers continue to invest in improving carbon black as an industrial raw material, still believing it to be a key part in maintaining tire quality. As the experts at Birla Carbon, a major supplier of carbon black products and a subsidiary of Fortune 500 company Aditya Birla Group, note, “Carbon blacks have been formulated to further reduce non-tread compound hysteresis and improve inner liner permeability that helps to increase tire life and fuel economy.”
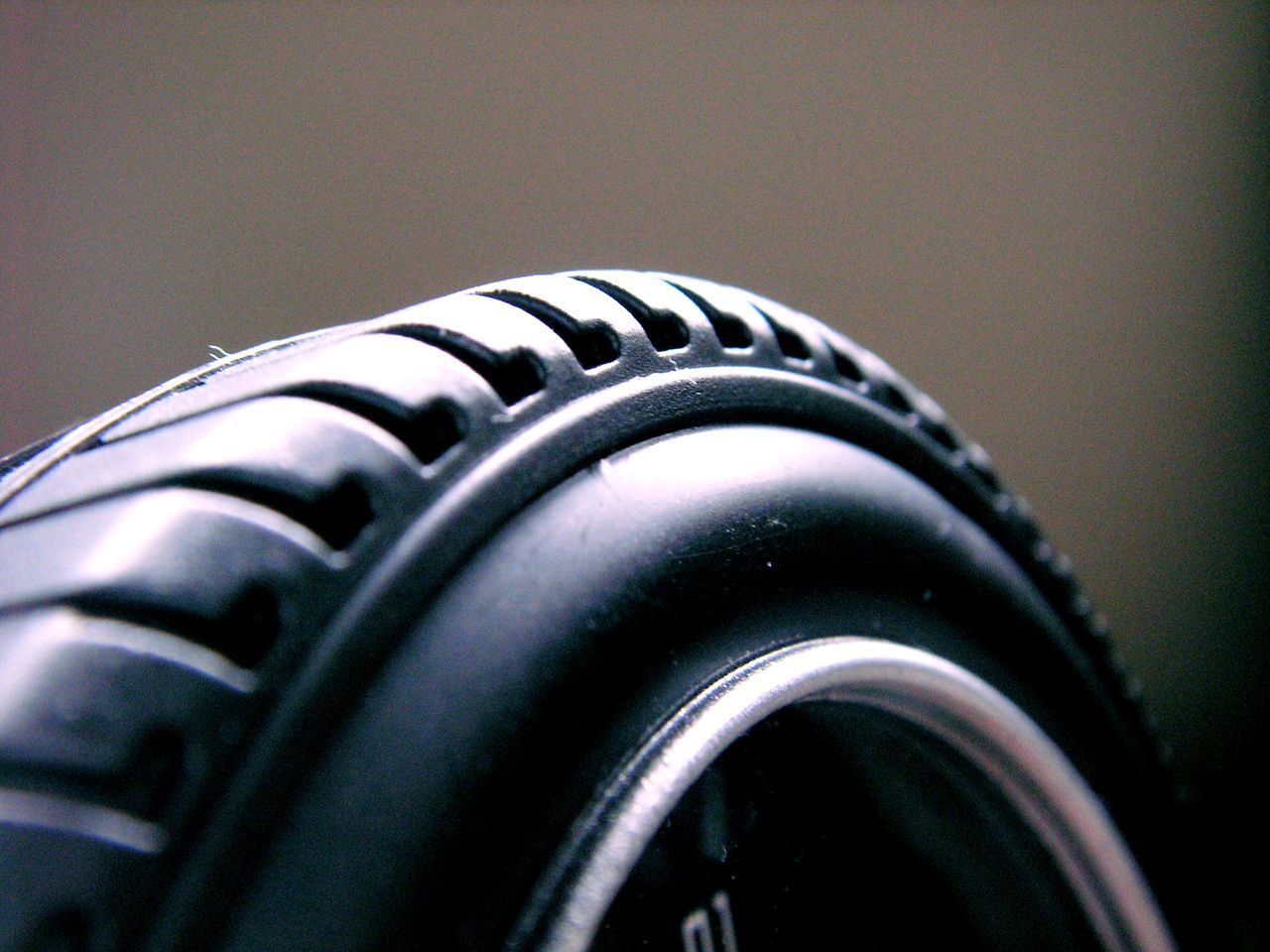
Adding that, “Our technology services teams are focused on developing new grades of carbon black for further improvements in treadwear and reducing heat build-up in the tread and non-tread components. These improvements can reduce CO2emissions, also improving fuel economy and tire life.”
But maybe they are focusing on the wrong raw material, as tire manufacturing may be about to change. Carbon black is being replaced by nanotechnology; specifically, single walled carbon nanotubes (SWCNT).
The nanotubes are only one atom thick (less than 100,000th of the width of a human hair), but their small size gives them very different properties to how raw materials behave at a macroscale.
Nanotechnology involves the use of materials on a minute scale (1mm = 1 million nanometres). The width of a human hair is about 100,000nm.
Materials used at such a tiny scale have different properties and special advantages over those used in bulk.
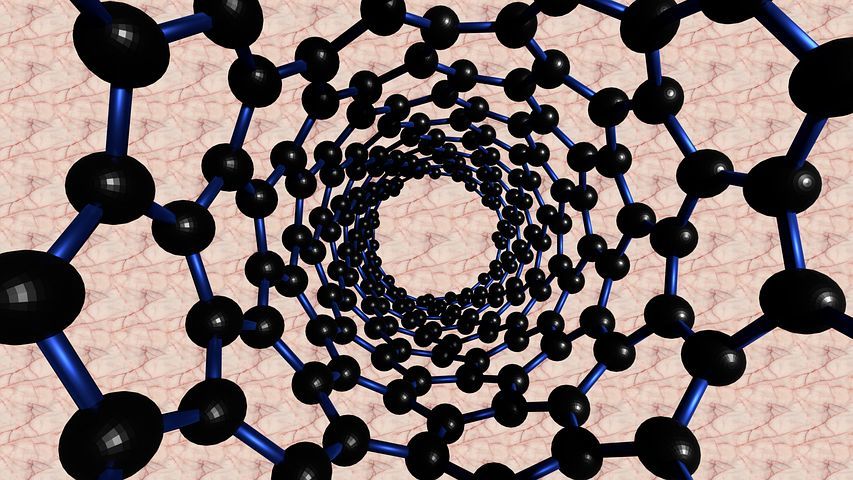
For example, a gold bar must be heated to 1,064oCbefore it starts to melt. But the same gold bar in a nanoform will melt at 591oC.
Similarly, gold (as an inert material that doesn’t corrode or tarnish) would normally be considered a silly material to use as a catalyst for chemical reactions. However, at a scale of 5 nanometres it can act as a catalyst for a reaction such as oxidizing carbon monoxide.
The American Chemical Society notes, that one of the most versatile applications of nanotechnology is nanotubes. Stating that, “Carbon nanotubes are one hundred times stronger than steel and yet also much lighter.”
Nanotechnology enables engineers to do things that were previously impossible, giving it real-world, practical uses.
But, while the science behind carbon nanotube technology is complex, the reasons for the change are clear.
By using single walled carbon nanotubes, the manufacturers are able to make a tire that is more durable, maintains black colour longer, has improved heat qualities, reduces the build-up of static-electricity, and requires a product input of as little as 1%.
A recent nanotube ingredient that entered the market in early 2018 has already been proven as a raw material that enables better performance in tires made of Natural Rubber (NR), Polybutadiene Rubber (BR), or even Styrene Butadiene Rubber (SBR).
By adding only 1% of SWCNTs during the manufacturing process tire manufacturers are creating tires that are lighter, have better wet grip and resistance to abrasion, lower rolling resistance, reduced heat build-up, and have increased electrical conductivity.
Nanotubes are also a more sustainable raw material, as they require less product per volume of rubber. They also lower fuel consumption by improving tire performance, making for a more eco-friendly tire.
While the addition of a new ingredient that takes up only 1% of a tire’s weight may seem like an insignificant change, the tire production industry is big money, with the largest tireproducing companies, Goodyear, Bridgestone, Michelin, Pirelli, and Continental, all being household names. Meanwhile, industry market research professionals at Freedonia estimate that, “World demand for tires is projected to rise 4.1 percent per year to 3 billion units in 2019. In value terms, sales of tires are forecast to advance 7 percent per annum to $258 billion.”
Single walled carbon nanotubes may represent only a small part of that industry, but the impact they will have is big business.
Photo credit: OCSiAl, USTires, Indycar, Tirereview, FaisanInternational, Nanotechmag, Hiveminer, & Orkhim