Nanotechnology researchers have discovered that it is possible to synthesize carbon nanotubes from sodium-based raw materials. Even household products such as table salt, detergent, and baking soda were found to have sodium-compounds suitable for carbon nanotube (CNT) production.
But even more interesting, was that the method used operated at a much lower temperature, giving a potential energy saving for industrialised carbon nanotube manufacturing. Additionally, it provides a breakthrough in allowing nanotubes to be grown on lower-temperature materials, such as polymers.
“In aerospace composites, there are a lot of polymers that hold carbon fibers together, and now we may be able to directly grow CNTs on polymer materials, to make stronger, tougher, stiffer composites,” says Richard Li, the study’s lead author and a graduate student in MIT’s Department of Aeronautics and Astronautics. “Using sodium as a catalyst really unlocks the kinds of surfaces you can grow nanotubes on.”
As Jennifer Chu of the MIT press office explains, “Researchers typically grow CNTs on various materials through a process called chemical vapor deposition. A material of interest, such as carbon fibers, is coated in a catalyst — usually an iron-based compound — and placed in a furnace, through which carbon dioxide and other carbon-containing gases flow. At temperatures of up to 800 degrees Celsius, the iron starts to draw carbon atoms out of the gas, which glom [attach] onto the iron atoms and to each other, eventually forming vertical tubes of carbon atoms around individual carbon fibers. Researchers then use various techniques to dissolve the catalyst, leaving behind pure carbon nanotubes.”
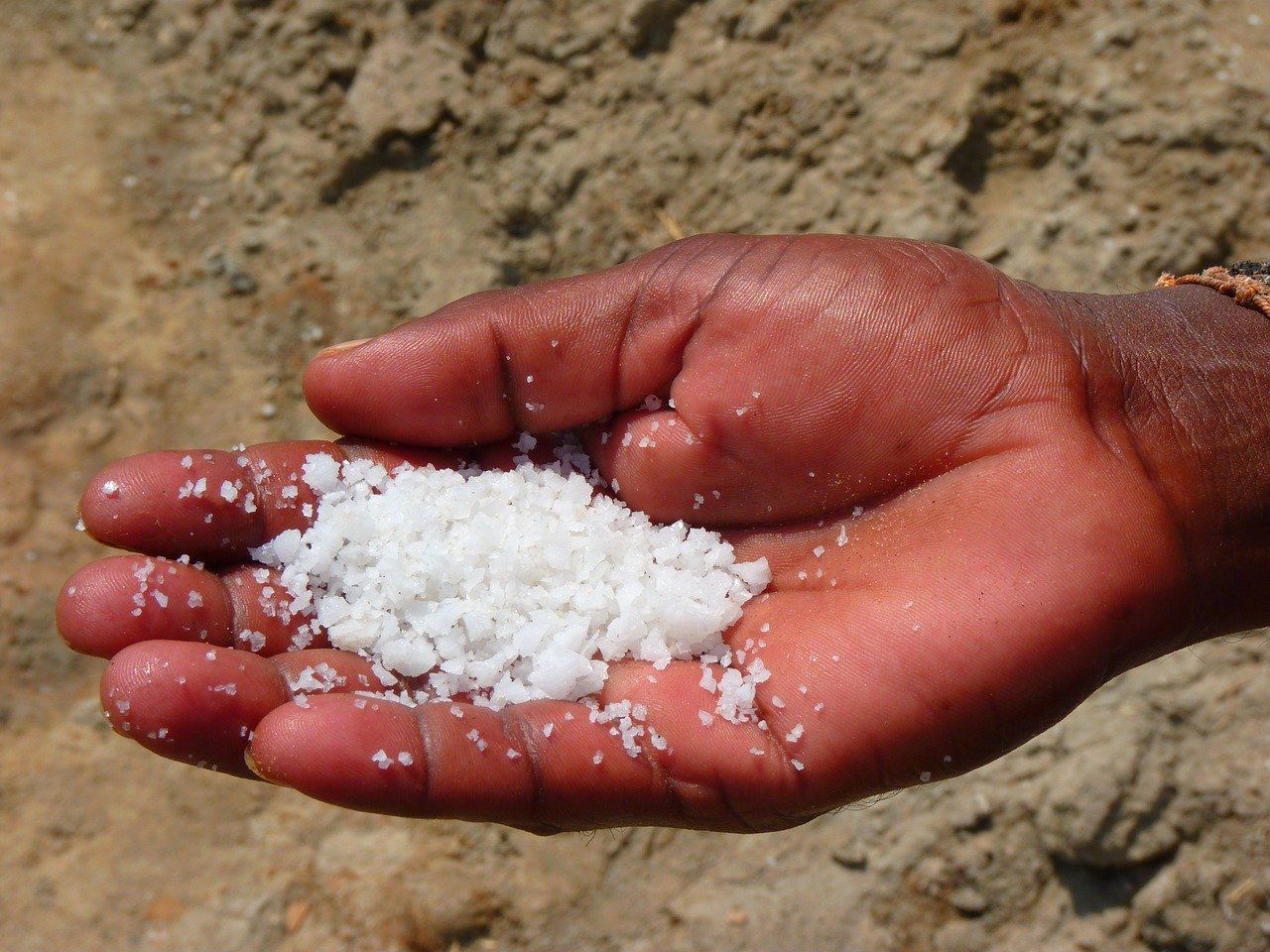
The new approach provided short, dense forests of carbon nanotubes at 480° C; more than 300° C lower than when using an iron-based catalyst. Moreover, after the forests were left in the furnace for 15 to 30 minutes, the sodium ‘simply vaporized away’, leaving only hollow carbon nanotubes behind.
The breakthrough came about when Li and his colleagues were experimenting on how to grow CNTs on various surfaces by coating them with solutions containing different levels and types of iron-containing compounds. The team was surprised to find that some of the carbon nanotubes looked different to what they would have expected.
As professor of aeronautics and astronautics Brian Wardle, who was a co-author of the study describes, “The tubes looked a little funny, and Rich and the team carefully peeled the onion back, as it were, and it turns out a small quantity of sodium, which we suspected was inactive, was actually causing all the growth.”
Excited by this observation, the team began to focus on other sodium-compounds, including those found around the house (salt, detergents etc.), before progressing to purer forms which they dissolved in water. They then immersed carbon fibres into the sodium solutions to coat the fibre’s surface. Finally, the fibres were placed in a furnace to begin the standard chemical vapor deposition process and carbon nanotube production.
“Sodium and other alkali metals have not been explored for CNT catalysis,” explains Wardle. “This work has led us to a different part of the periodic table.”
The team’s results have now been published in the journal Angewandte Chemie, where they explain in detail how they have achieved, “… high‐yield thermal chemical vapor deposition (CVD) synthesis of CNTs catalyzed by reagent‐grade common sodium‐containing compounds, including NaCl, NaHCO3, Na2CO3, and NaOH, found in table salt, baking soda, and detergents, respectively.” Adding that, “Coupled with an oxidative dehydrogenation reaction to crack acetylene at reduced temperatures, Na‐based nanoparticles have been observed to catalyze CNT growth at temperatures below 400 °C.”
This significantly lower cooking temperature and the way that the sodium catalyst vaporizes away is certain to attract the attention of industrial carbon nanotube manufacturers. As it reduces energy usage and removes the step of cleaning off an iron-based catalyst.
As Wardle observes, “A large part of CNT research is not on growing them, but on cleaning them —getting the different metals used to grow them out of the product. The neat thing with sodium is, we can just heat it and get rid of it, and get pure CNT as product, which you can’t do with traditional catalysts.”
The discovery has heralded a new phase in research, as nanotechnology specialists will further develop the use of sodium as a raw material for making CNTs. For now, the nanotubes made from sodium have not been of exceptionally high quality, with the hexagonal patterns on the wall not perfectly aligned. The team hope to improve the quality with further experiments, such as altering the time in the furnace, the concentration of the sodium solution, the temperature, and numerous other conditions.
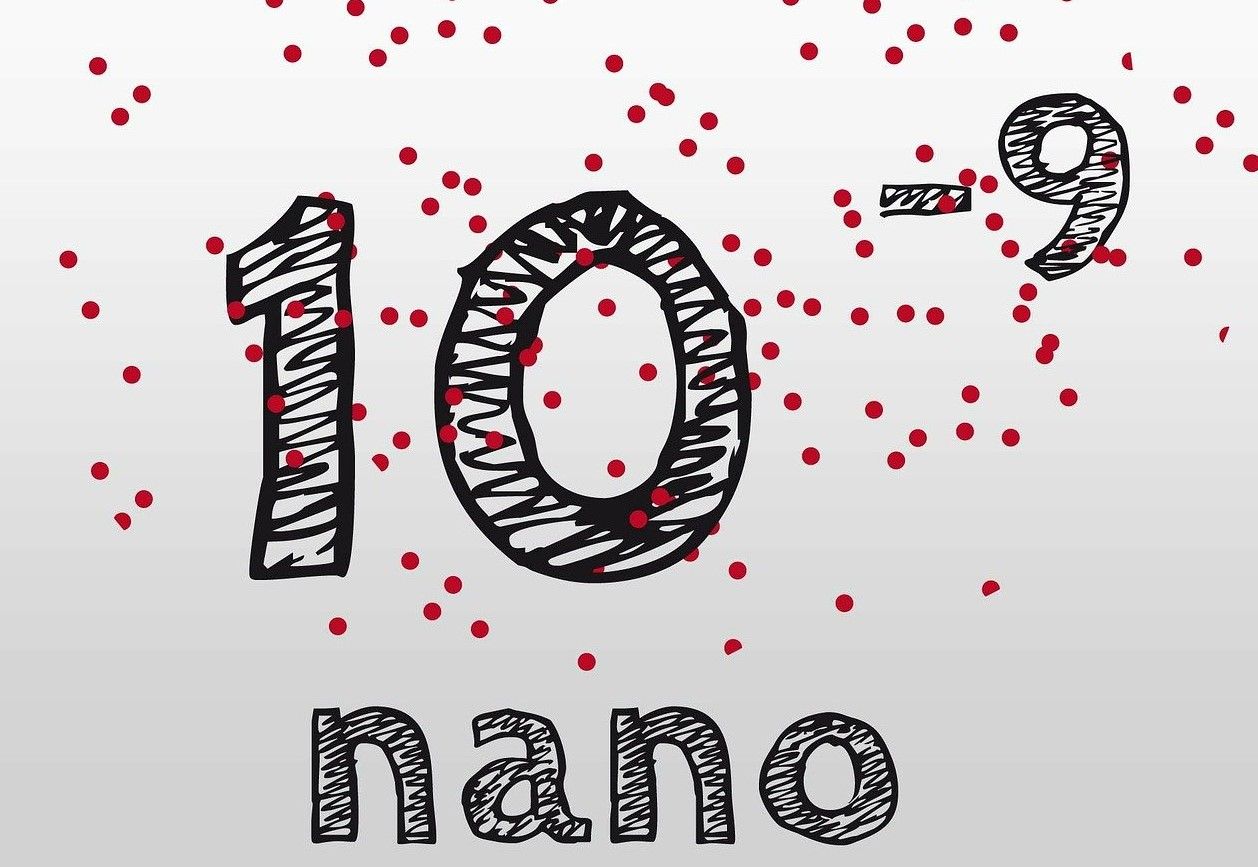
As Li made clear when he said, “There are so many variables you can still play with, and sodium can still compete pretty well with traditional catalysts.”
In fact, the ability to use sodium as a carbon nanotube catalyst has sent shockwaves across the industry, and a plethora of activity to discover what new properties and applications sodium-based nanotubes may yield.
“It is a surprise that we can grow carbon nanotubes from table salt!” says Shigeo Maruyama, professor of mechanical engineering at the University of Tokyo, who was not involved in the research. “Even though chemical vapor deposition (CVD) growth of carbon nanotubes has been studied for more than 20 years, nobody has tried to use an alkali group metal as a catalyst. This will be a great hint for the fully new understanding of growth mechanism of carbon nanotubes.”
These are interesting times for the nanotechnology industry, as new processes of CNT manufacturing, new nanotube products, and new raw materials continue to be found. The ability to employ such commonplace ingredients as table salt may reveal new insights into the way these exceptionally strong and versatile materials grow.
As Li notes, “We anticipate with sodium, it is possible to get high quality tubes in the future. And we have pretty high confidence that, even if you were to use regular Arm and Hammer baking soda, it should work.”
Exciting times indeed!
Photo credit: MIT, Universtyofcambridge, Autodesk, Indiamart, Joshgitalis, Tomshardware, & Assemblymag