A new approach to ammonia production is asking questions of nanotechnology specialists to see if fertilizer production can be cheaper. The inorganic chemical reaction is more energy efficient than the Haber-Bosch process, and is also possible under ambient pressure and room temperature. Furthermore, it does not produce carbon dioxide as a waste product, making it more environmentally friendly.
The breakthrough was based on a two-dimensional crystal called molybdenum disulphide. By removing sulphur atoms from the crystal’s latticelike structure the team was able replace the now exposed molybdenum with cobalt.
The result is a catalyst that can copy the natural organic process of turning atmospheric dinitrogen into ammonia.
In nature, this is performed by bacteria inside organisms, for example, in humans it makes ammonia for healthy liver function.
While the research’s lead scientist, Jun Lou, acknowledges that the process, as it stands, will not be used for large-scale fertilizer production, the discovery has opened the door for further research into how nanomaterials can be manipulated to solve industrial chemical problems. It may also yet lead to a replacement for the Haber-Bosch process, known for its poor environmental record.

“The Haber-Bosch process produces a lot of carbon dioxide and consumes a lot of energy,” says Xiaoyin Tian, the study’s co-lead author. “But our process uses electricity to trigger the catalyst. We can get that from solar or wind.”
The research was conducted at the Brown School of Engineering at Rice University, and was based on the team’s good understanding of molybdenum disulphide and the way that it bonds with dinitrogen, a molecule made up of two strongly bonded nitrogen atoms that forms almost 80% of the air that we breathe.
As the university press release explains, “Computational simulations by Mingjie Liu, a research associate at Brookhaven National Laboratory, showed replacing some exposed molybdenum atoms with cobalt would enhance the compound's ability to facilitate dinitrogen's reduction to ammonia.”
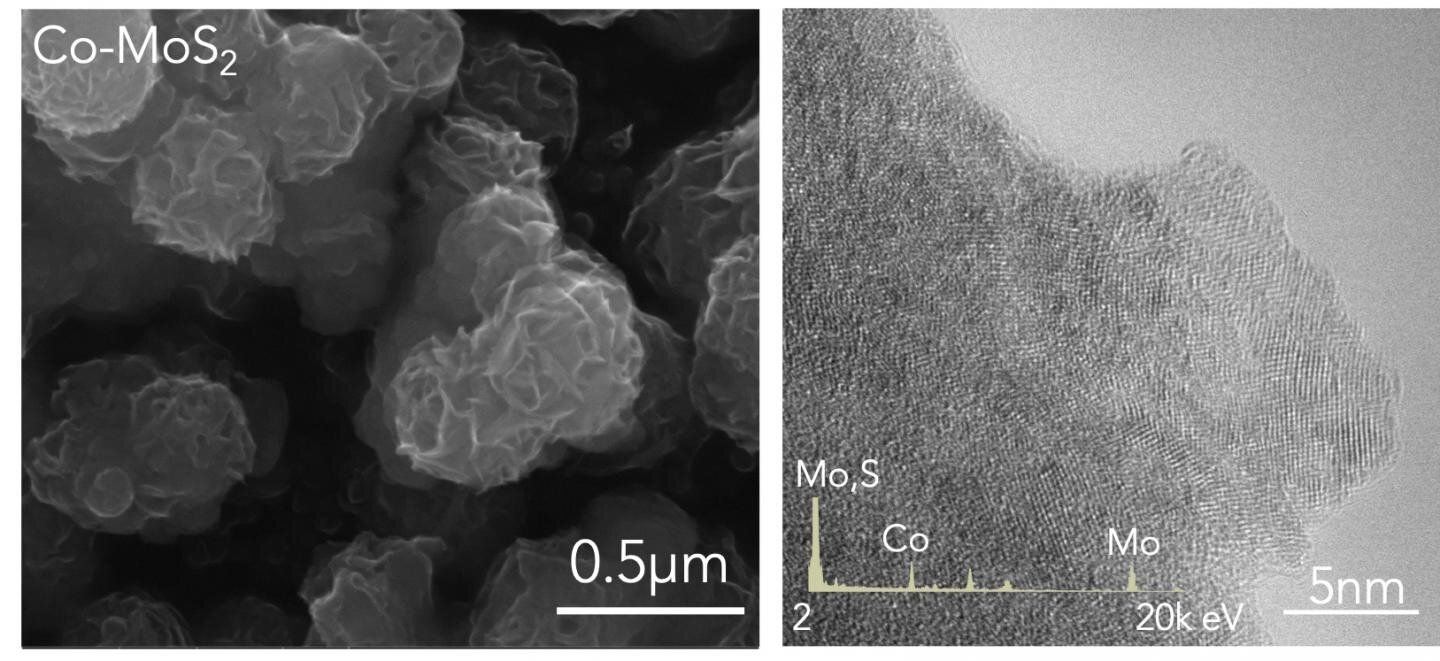
The theory and computer predictions were then supported by tests carried out in the lab. As the report further outlines, “The researchers assembled samples of the nanoscale material by growing defective molybdenum disulfide crystals on carbon cloth and adding cobalt. (The crystals are technically 2-D but appear as a plane of molybdenum atoms with layers of sulfur above and below.) With current applied, the compound yielded more than 10 grams of ammonia per hour using 1 kilogram of catalyst.”
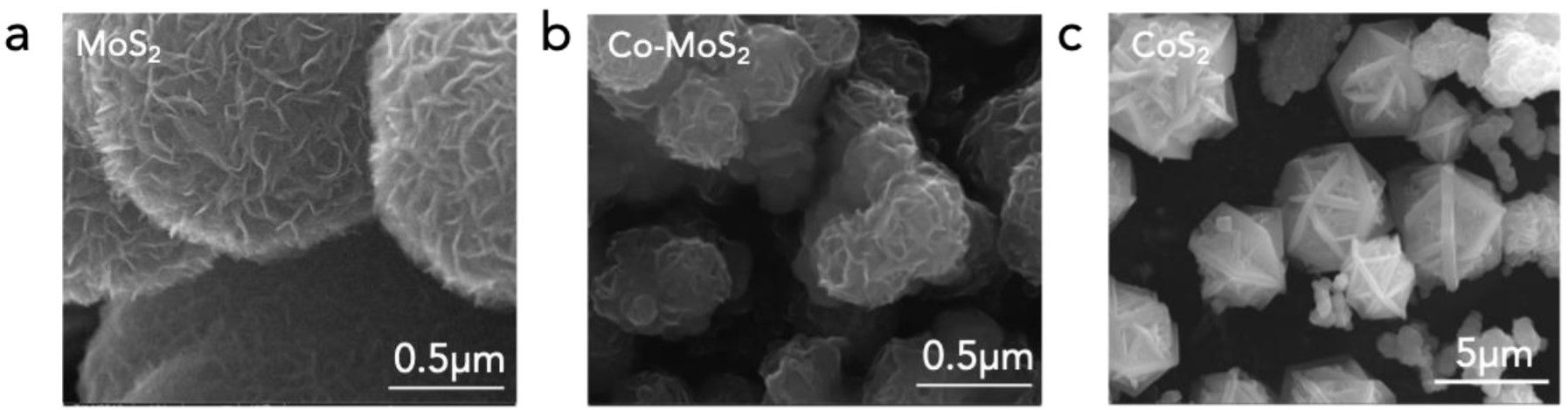
While the lab experiments used a direct supply of dinitrogen, the platform is capable of extracting the raw material straight from the air.
The study has now been published in the Journal of the American Chemical Society.
While the use of the cloth will prevent the method being used to produce the 450 million tonnes of anhydrous ammonia made by the Haber-Bosch process every year, it does provide a new option.
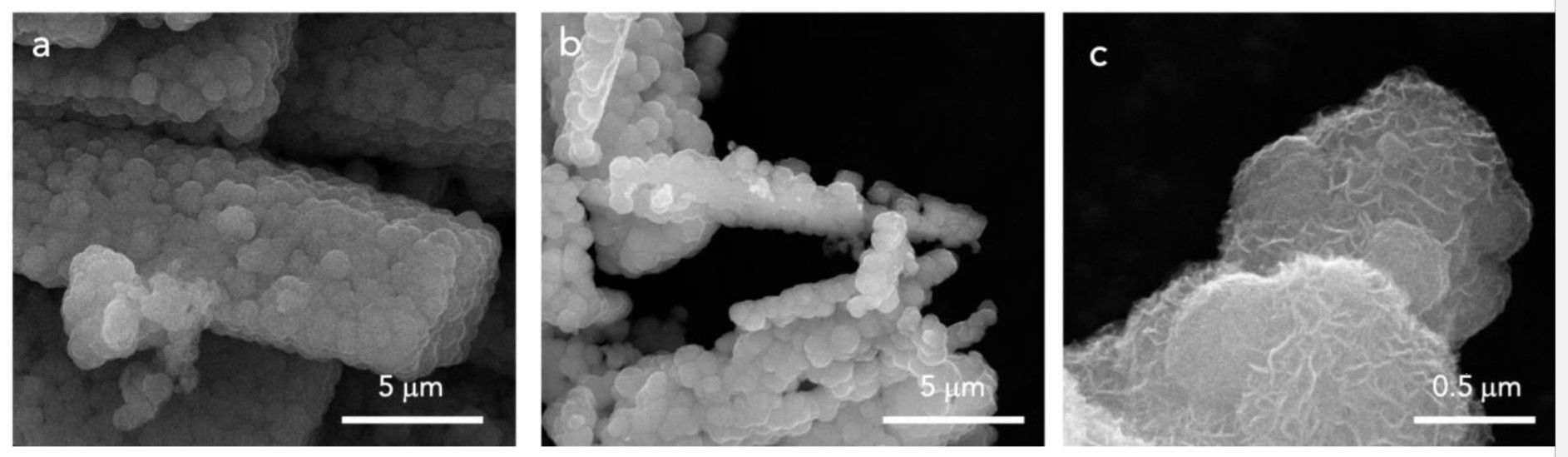
A point highlighted by Jing Zhang, a co-lead author on the work, when she noted that, “The scale is not comparable to well-developed industrials processes, but it can be an alternative.” Specifically, “It will allow the production of ammonia where there is no industrial plant, and even in space applications.”
Work is now continuing to see if different dopants can create other novel catalysts, especially those that could produce other valuable chemical raw materials, besides ammonia. The hope is to use more nanomaterials to copy what bacteria do every day to further boost the nanofertilizer industry.
“We thought there was an opportunity here to take something we're very familiar with and try to do what nature has been doing for billions of years,” says Lou. Before adding that, “If we design a reactor the right way, the platform can carry out its function without interruption.”
Using nanotechnology to create never ending production of ammonia from atmospheric nitrogen? Sounds like something that the fertilizer industry could well be interested in.
Photo credit: JournaloftheACS, Spectator, & RiceUniversity