The design of modern composites often involves looking to biology to see how Mother Nature makes the planet’s strongest, most flexible, hardest, or most durable substances. Today, bioinspired engineers are using nanotechnology to mimic natural materials, and in doing so make the most advanced composites known to man.
One natural material that has often captured the imagination of material scientists is nacre, also known as mother of pearl.
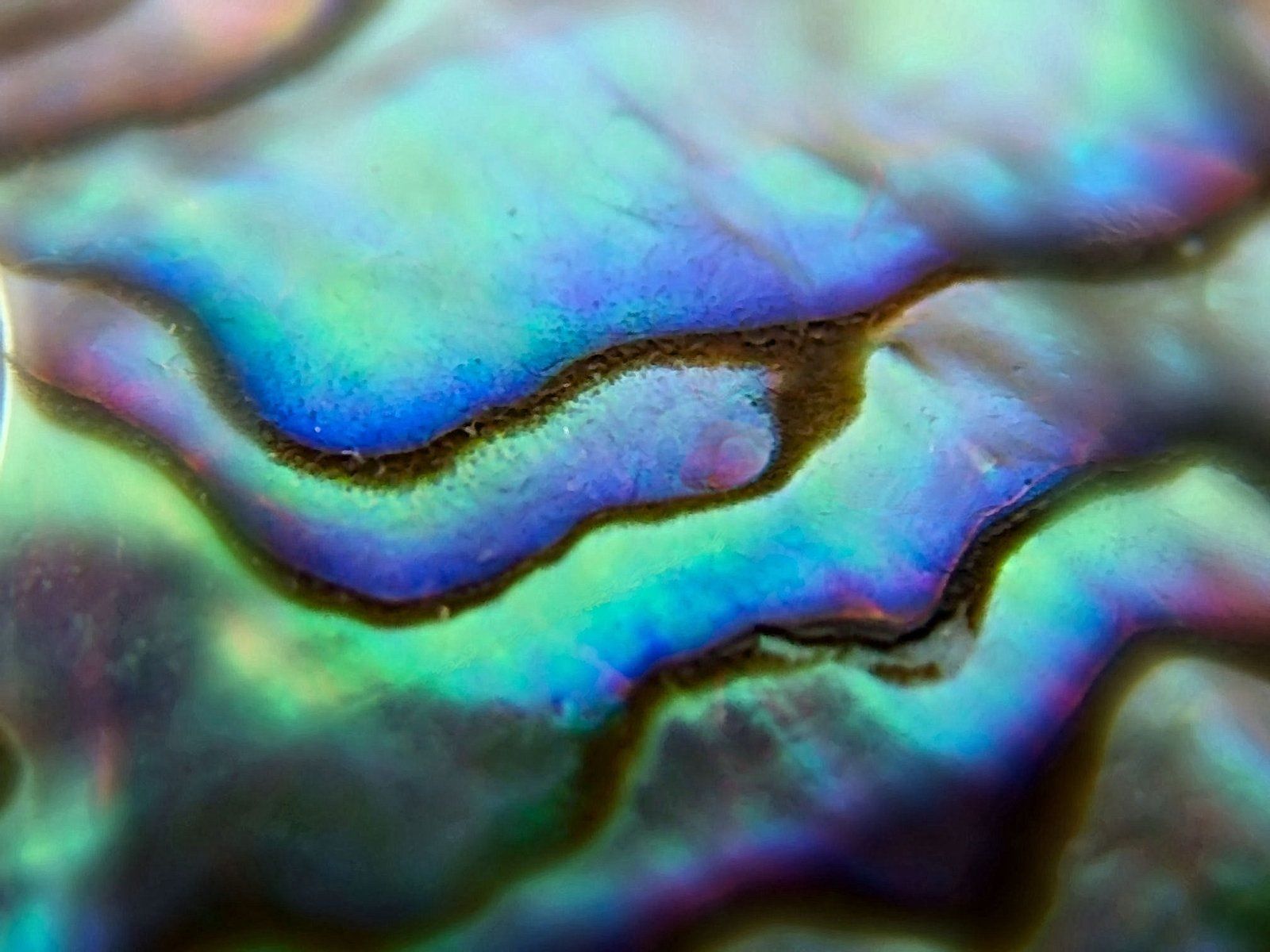
Nacre, as well as being an exceptionally durable, and rigid material also has a high level of ductility. This means that for such a hard substance it is still able to bend and be distorted in shape with minimal fracturing. This ‘un-brittleness’ combined with its other properties makes it unlike any synthetically manufactured material.
Naturally formed nacre is composed of aragonite platelets (in the form of CaCO3) and a biopolymer. These are formed together as a ‘brick-and-mortar’ structure, with the platelets working as bricks to provide strength, while the biopolymer binds them together like a mortar.
While surprisingly simple in design, this formula provides the strength and ductility that material engineers are looking for. A substance made up of mineral bridges which can shield against fracturing, while a polymer layer dissipates the fracture energy to prevent large-scale cracks.
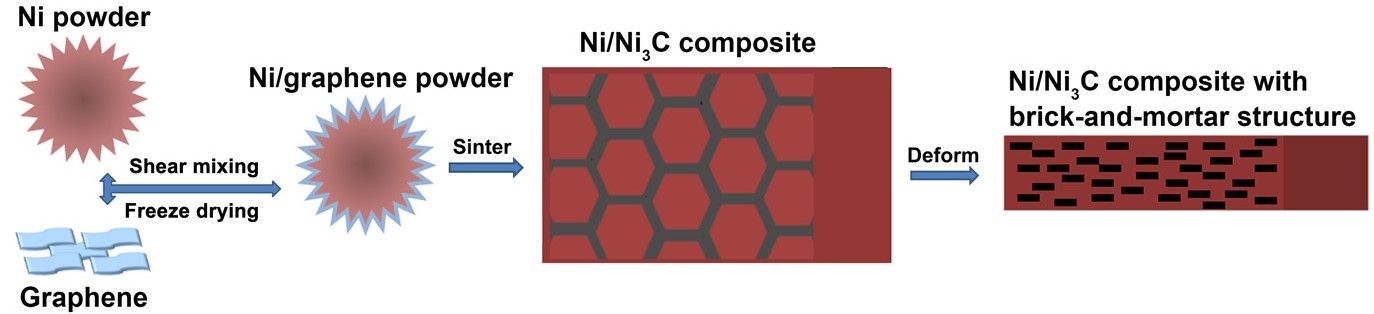
Based on this principle, material scientists have been working for years on how to recreate what nature has in nacre’s ‘bricks-and-mortar’ structure. To date, they have met with only partial success, as Phys.org explains, “Previous attempts to mimic the architecture of nacre had remarkable success. However, the intrinsically low plasticity of ceramics and polymers used, limited their potential mechanical activity.”
It was at this point that Yunya Zhang and a team based at Northwestern University and the University of Virginia employed Ni powders combined with graphene sheets to create a nacre-inspired Ni/Ni3C composite.
The details of the new composite production process have now been published in the journal Science Advances, where the researchers describe how, “Graphene closely wrapped Ni powders via shear mixing and freeze drying. The Ni/graphene powders were compressed and sintered at 1450°C, forming Ni3C at the grain boundary area. They were rolled into long stripes during the cold deformation, leading to the formation of a brick-and-mortar structure. Additional carbon atoms were dissolved into the Ni matrix and existed as interstitial solution atoms. The Ni3C platelets not only acted as the load bearers but also redirected crack propagation.”
The result was a significantly stronger material that had the additional ability to limit fracturing. As the study states, “The small grains and interstitial solution atoms prohibited the dislocation propagation and enhanced the Ni matrix. In total, the confluence of multiple strengthening and toughening mechanisms enabled a 73% increase on strength … with only 28% reduction in ductility, leading to a 44% improvement in toughness.”
Adding that the new, “Ni-Ti-Al/Ni3C composite exhibited superior strength over commercial superalloys up to 1000°C.”
Much has already been written about the exceptional qualities that graphene possesses, but this example of how nanomaterials can be developed to create novel composites shows the true potential behind nanotechnology. Combining old theories with natural designs and modern nanomaterials for improved raw materials.
While the team are continuing their studies, the results of this research is sure to capture the interest of many composite manufacturers. A robust, strong, durable, and non-brittle polymer has many potential applications in the aerospace industry, high-end plastic production, the automobile industry, military equipment manufacturing, and construction.
All of which makes the addition of a new nanomaterial based composite big business, with the American Composites Manufacturing Association reporting that, “… composites manufacturing is a $25 billion a year industry in the United States.”
Ultimately, the team have found a new way to incorporate nanomaterials into nature-inspired designs, with the possibility of further discoveries being made. As the study concludes, “This strategy presents a new promise for the design and synthesis of advanced bioinspired materials to achieve exceptionally high mechanical robustness for applications in an extensive range of fields.”
Photo credit: ScienceAdvances, Mewburn, & Pinterest