Further evidence came to light recently of the growing power of nanotechnology as a team of researchers from the University of Pennsylvania have developed a form of ‘Nano-Cardboard’. Made from an aluminium oxide film with a thickness of tens of nanometres the new structure is the ultrathin equivalent of corrugated paper cardboard.
Given cardboard’s strength yet lightweight properties, the decision to copy its structural design was relatively simple. As Igor Bargatin, an assistant professor of Mechanical Engineering and Applied Mechanics, who co-led the study, explains, “Corrugated cardboard is generally the sandwich structure people are most familiar with. It's ubiquitous in shipping because it's both lightweight and stiff. But these structures are everywhere; the door to your house is probably a sandwich structure, with solid veneers on either side and a lighter core, such as honeycomb lattice, on the interior."
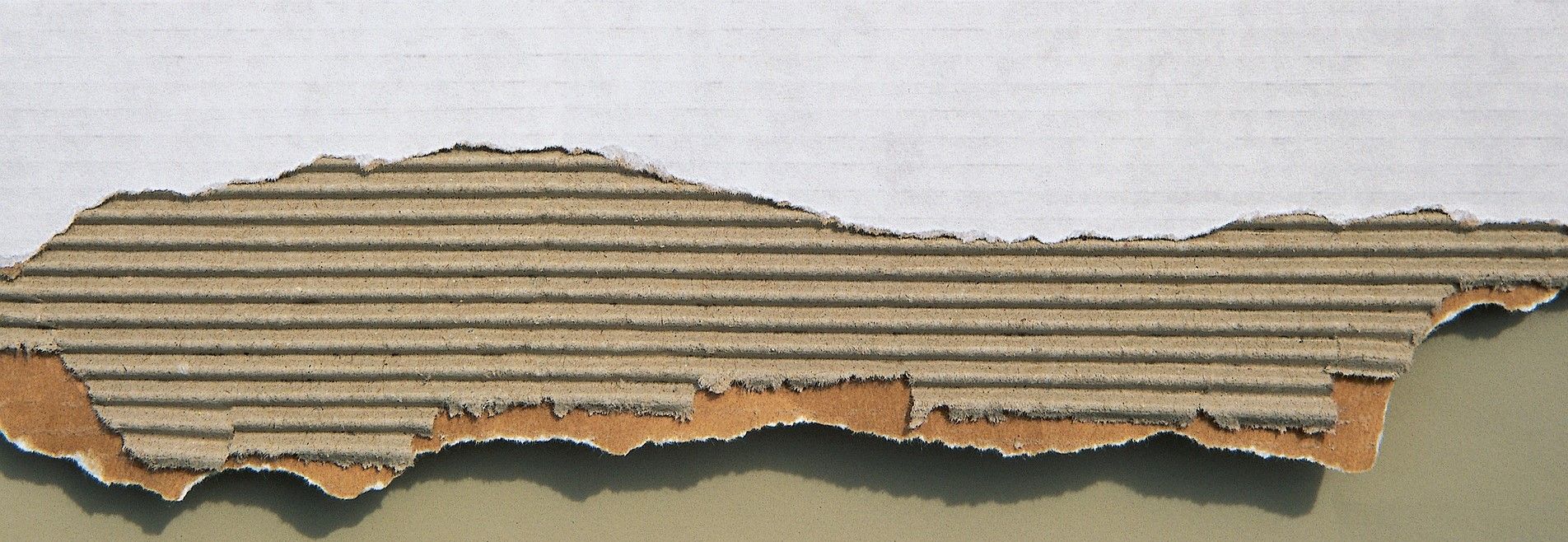
But the researchers also took inspiration from nature in finding the best way to align the tubes supporting the material. As co-lead researcher Samuel Nicaise notes, "Not surprisingly, evolution has also produced natural sandwich structures in some plant leaves and animal bones, as well as in the microscopic algae called diatoms."
However, creating cardboard on a nano-scale still took a lot of trial and error to find the correct raw materials and the strongest, yet most flexible, design. "At the macroscale," Bargatin says, "you can just glue the face sheets and the lattice together, but at the nanoscale, the structures we work with are thousands of times thinner than any layer of glue you can find."
While considering how to join the two planes, the researchers met Gerald Lopez and Meredith Metzler who were working at the Singh Center for Nanotechnology. One of their jobs there was to manufacture microscopic filters that could remove minute tumour cells and macrophages from blood.
One of the problems that they faced was that many of the filters they made were too floppy for practical use. "Our solution,” notes Metzler, “was to pattern our filters using a thin sheet of silicon over glass." The result was a reliable method for making filters that were much stiffer, yet still only nine microns in diameter and a hundred microns deep.
When Metzler and Lopez heard of the plan to make nano-sized cardboard, the idea of how to create nano-cardboard was formed.
As the scientific journal Phys.org, describes, “The process involves making a solid silicon template with channels running through it. Aluminium oxide can then be chemically deposited in a nanometer-thick layer over the silicon. After the template is encased, the nano-cardboard can be cut to size. Once the sides are exposed, the silicon on the inside can be etched away, leaving a hollow shell of aluminium oxide with a network of tubes connecting the top and bottom faces.”
However, as the report notes, the researchers still faced challenges, “The team's first design featured distantly spaced circular channels going through the sheets, much like the blood filter. But despite simulations predicting that it would provide the optimal stiffness, these first designs failed.”
“The problem was that wrinkles would randomly form along the lines between those channels," Bargatin says. "Whenever we tried to measure their properties, we'd get unrepeatable results.”
In response, the team experimented with different structural shapes and finally settled on a “basket-weave pattern, featuring close-set, slit-shaped channels arranged in alternating directions”. This shape discouraged wrinkles forming while also gave the material toughness under extreme bending.
The final product has unique thermal properties, as well as a high surface area, but its the mechanical abilities that truly surprise.
“If you apply enough force, you can bend corrugated cardboard sharply, but it will snap; you'll create a crease where it becomes permanently weakened,” Bargatin explains. “That's the surprising thing about our nano-cardboard; when you bend it, it recovers as if nothing happened. That has no precedent at the macroscale.”
The team have now published their findings in the journal Nature, where they describe they define the materials flexibility, stating that, “Even after taking into account the shear [of the bend], the nano-cardboard plates with optimal webbing parameters offer spring constants that are four to five orders of magnitude larger than that of solid plates of the same areal weight.”
Future research will focus on some of the material’s other amazing properties, including the way that light can make the nano-cardboard levitate. This is due to the light on one surface creating heat that is not transferred to the other side. This forces a current of air molecules out through the bottom, causing the nano-cardboard to ‘float’.
While such a novel material has yet to find a practical application, investors are already considering its potential. Possible applications include;
- using its stiffness-to-weight ratio for aerospace and micro-robotic applications
- using nano-cardboard for constructing the wings of ultralight micro-flyers
- in probes for measuring and moving other nanotechnology (Atomic Force Microscopy or AFM)
- for making a ‘light sail’ for interstellar travel
- using its high surface area, robustness and high flexural resonance frequency in chemical sensors
- in the manufacture of acoustic metamaterials
- in the manufacture of high-temperature thermal insulation (as it is mostly empty space)
- Or for use in other micromechanical systems with vacuum, gas, and liquid environments
But beyond these real-world uses, nano-cardboard provides manufacturers with a material of incredible strength, flexibility, and low-weight. It is also further proof of nanotechnology’s potential, as it shows the vast range of new properties that can be obtained not by using new raw materials, but by reconfiguring known substances on a nanoscale.
Photo credit: University of Pennsylvania, Nature Communications, Phys.org & Wikipedia